Hello all, Sorry to resurrect an old thread, but I'm still utterly confused by the bearing arrangement in the knucklehead ad how to apply the correct preload.
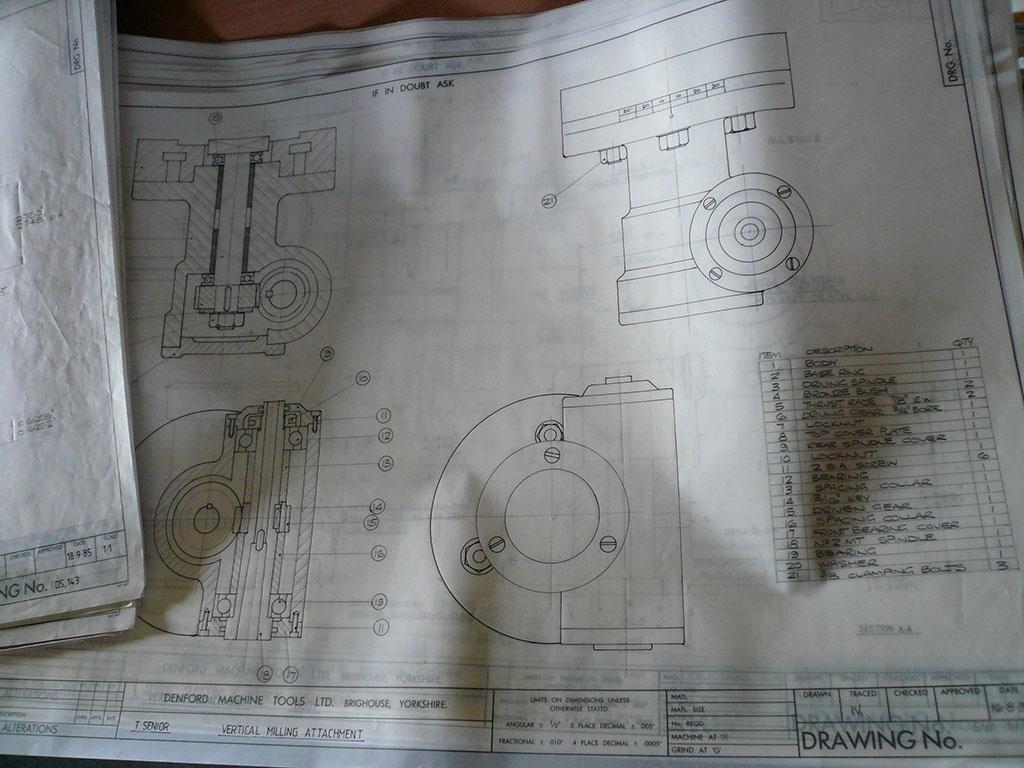
Looking at the drawing in the bottom left, it would appear that (with no shoulder for the outer shells to push against) the nut on the spindle only serves to clamp the bearing inner shells, spacing collars and driving nut against each other. This does not provide any preload adjustment, infact it could serve the opposite by unloading the angular contact preload when tightened up depending on the outer shell positions.
One way of setting preload could be the action of the end caps pushing in on the outer races of the bearings through the use of some spacers, but this doesn't feel right.
another method of applying preload could be to make sure the bearing outer shells butt up against the end caps then shimming the inner spacing collars until the right preload is achieved.
Both of the above methods require using the end caps as the immovable object for the preload to act against which doesn't feel right due to their small retaining screws.
Do angular contact bearings work with no, or negative preload?
If you just assemble the spindle by pulling/pushing in the bearings and shaft, then tighten the retaining screw, and actually manage to gain some preload through the action of pressing in the outer shells so they are tight, then over time with the vibrations of cutting, wont the outer bearing shells relax and any preload you did have, would disappear.
I'm totally confused. I think the spindle guy must have been on annual leave when they came up with this design.
Any more thoughts?