Andrew it must be that builders merchants studding that comes up soo undersize
Just measured a bit of M8 and it comes out a 7.67mm , I've also had M12 where the crests were so flat due to it being indersize that it looked more like ACME form but the resin bonding method can be quite forgiving
I think a lot of it comes down to expeciance and the job in hand, for example the other day I was making and fitting some bearing caps fort ahit & miss engine. I drilled the tapping hole sin teh engine 4.00mm which is my usual size for 2BA but I also needed a simple jig to screw them to for some machining and I drille dthat 4.2mm as it only had to hold them the once and there was not a lot of load.
I think we have been down the bolt pull out route before, can't remember what the tapping size was for this M8 thread but the 7.8mm overall dia bolt came off better than the steel plate.

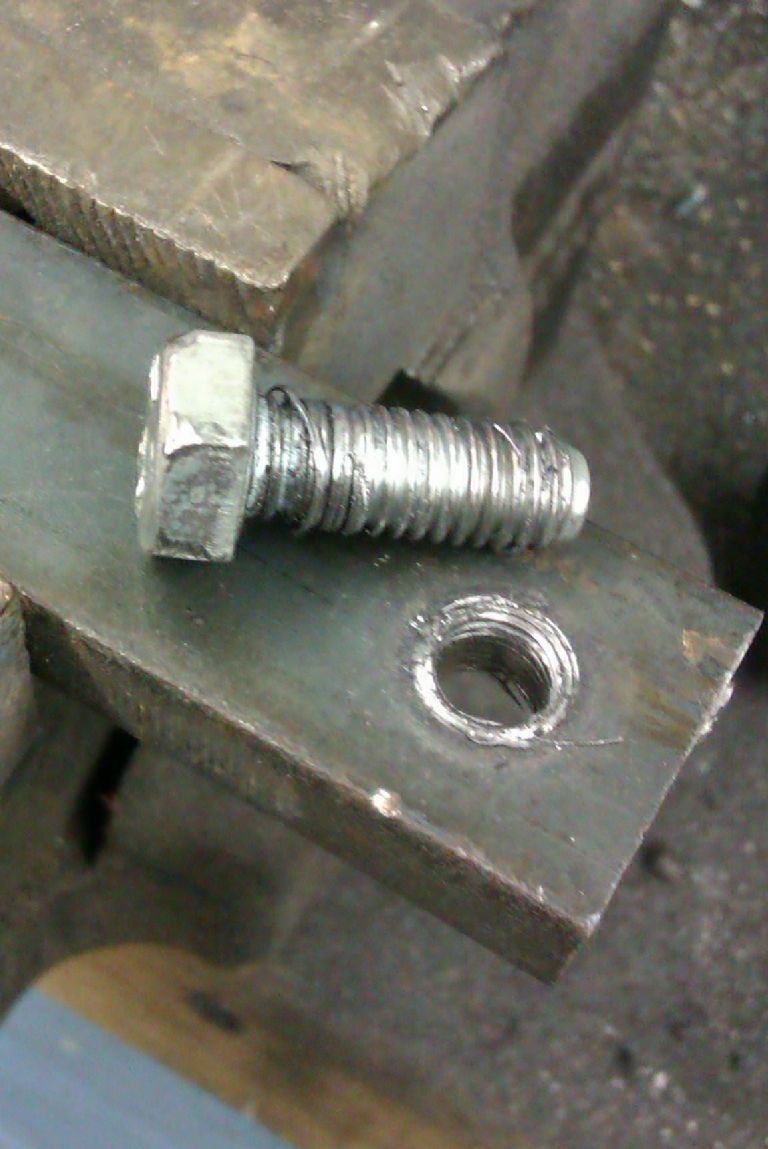

EDIT, I just found the old post, it was 10mm thick mild steel drilled 7.1mm rather than my usual 6.8mm.
Another interesting snippet from that post for those using TC tapping sizes is that the die should cut a full thread not an undersize one!! Which suggests his % engagements only apply when the male part is on size so if your male part is small alter your hole to suit.
Edited By JasonB on 11/10/2016 18:34:32