It looks like we’ve lost a piece!
404: Page not found
This page could not be found. Maybe try a search?
If it’s a forum topic you are looking for, some of our topics have moved, you can look for them in our new forum here.
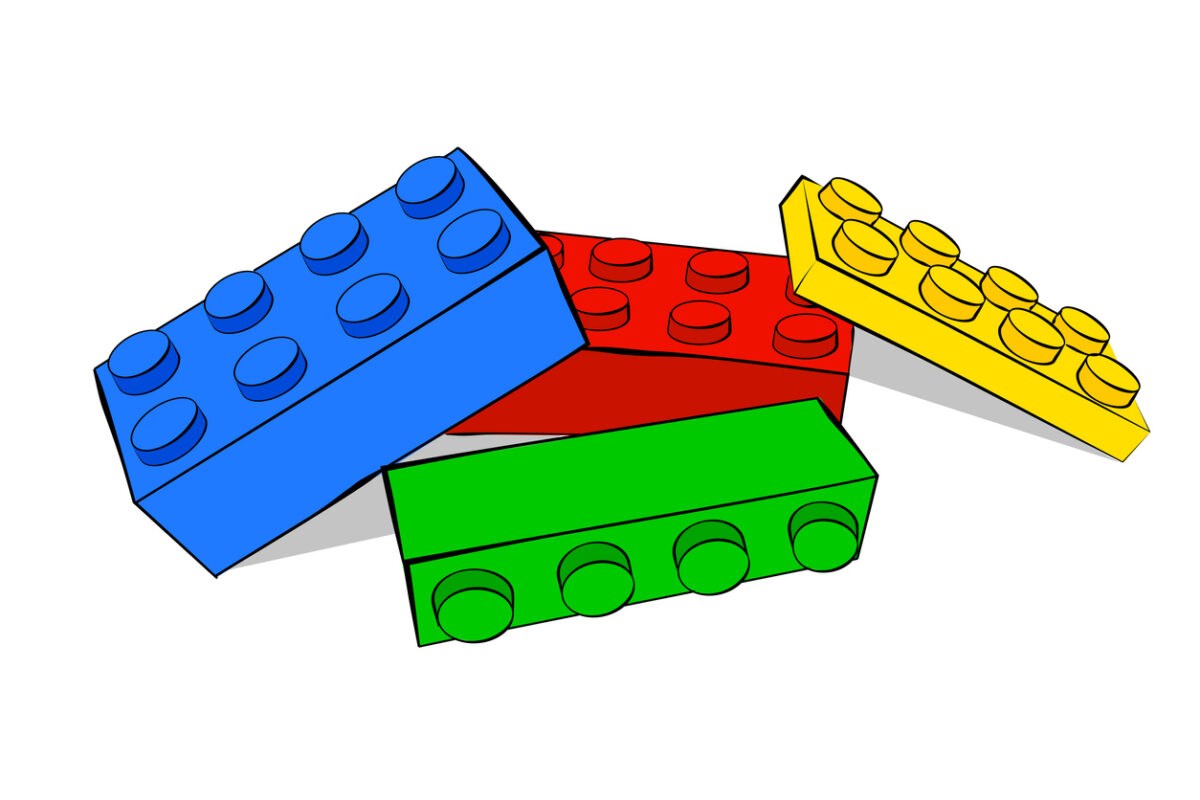
This page could not be found. Maybe try a search?
If it’s a forum topic you are looking for, some of our topics have moved, you can look for them in our new forum here.